Hi junkers !
This is my first stepper motor driver circuit .At this stage I don't know microcontrollers. Hence I am using four D flip-flop in its logical circuit. Using a J-K flip flop IC to build a D-flip flop. First of all you should know some basics about stepper motor. The stepper motor is different from a DC motor
because of its following characteristics.
1>Its speed and displacement can be accurately controlled using timing circuit.
2>It generally has high torque.
3>Less efficient as compared to DC motor.
4>Easy to control using microcontrollers.
5>:Has mechanically robust and sturdy design.
There are basically 2 types of stepper motors.
1>Unipolar[5 wires](old design and easy to drive but heavy and less torque). Polarity of the coil need not to be changed in order to move the motor in one direction.
2>Bipolar [4 wires](new design and hard to drive but light and more torque). Coil polarity needs to be changed. i.e. you will need a H-Bridge driver to drive it.
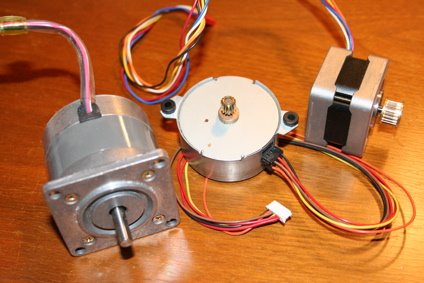
These motors are quite costly nearly INR 250 and above (in Indian market). Hence a better way to get it is to get if from a printer service station or scrap market (electronics market generally printers).
The two logical ways the motor runs is as follows and to get more torque you have to excite both coils at the same time.
let the minimum torque be "X"
then the logic sequence is
[1][0][0][0]
[0][1][0][0]
[0][0][1][0]
[0][0][0][1]
now to get torque 1.44 times two coils are to be exited at the same time
therefore the torque increases to "1.44X"
[1][1][0][0]
[0][1][1][0]
[0][0][1][1]
[1][0][0][1]
component list:
ic 7473 JK flip flop-2
ic 7404 NOT gate -1
ic 555 timer ic-1
ULN 2003 stepper moter driver ic-1
5V power supply-1
12v power supply-2
LED's-4
resistors
10k-1
20k-1
capacitor 1 uF-1
PCB linear-1
Ic base 16pin-1,14pin-3,8pin-1.


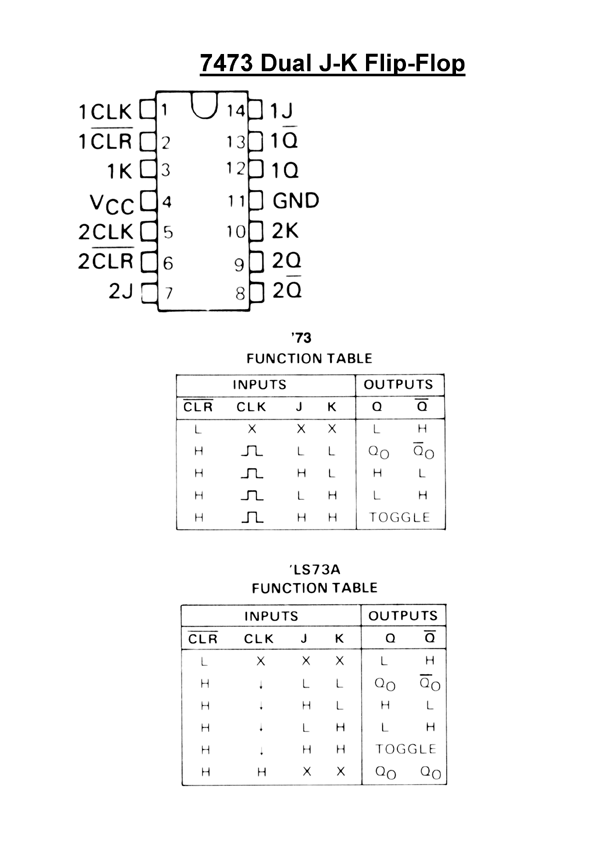
The circuit is quite simple. Basically a ring counter connected to a driver. The timing is controlled using IC555. A timing pulse is used to control the rpm of motor using ic 555 in astable mode (its operation is well discussed in IR remote control module) and a unipolar ULN2003 is used for driving the motor.

This circuit will work. Basically its a 4 bit ring counter connected to a motor driver. At this stage, I do not know how to use a schematic editor. I will post a better schematic once I learn to use it.
At all D connections of the circuit we connect the motor driver IC. Refer following link for generating a clock signal.
The astable output shown in link above is used as a clock signal.
Don't try to directly drive the motor using the flip flop signals. This is because the JK floip flop can source so less current (mA) that the voltage drops to zero when directly connected to motor.
Trouble shotting ?
1> The motor is just vibrating:
This is a verv common problem. To solve it you will have to increase the time period of the clock pulses.
i.e. decrease the frequency of timing pulses because the stepper motor take some finite time to rotate because of the rotor inertia.
2> The motor is running in zig zag pattern; check the logic sequence